The Scientific Research Behind Porosity: A Comprehensive Overview for Welders and Fabricators
Comprehending the elaborate mechanisms behind porosity in welding is critical for welders and producers aiming for impressive workmanship. As metalworkers explore the midsts of this phenomenon, they uncover a globe regulated by various variables that affect the development of these small gaps within welds. From the make-up of the base products to the complexities of the welding process itself, a wide range of variables conspire to either intensify or minimize the presence of porosity. In this thorough guide, we will certainly unwind the science behind porosity, exploring its results on weld top quality and unveiling progressed techniques for its control. Join us on this trip via the microcosm of welding blemishes, where precision meets understanding in the quest of flawless welds.
Recognizing Porosity in Welding
FIRST SENTENCE:
Assessment of porosity in welding reveals important understandings into the stability and top quality of the weld joint. Porosity, characterized by the presence of cavities or spaces within the weld steel, is a common concern in welding processes. These spaces, if not effectively dealt with, can jeopardize the architectural honesty and mechanical homes of the weld, causing possible failures in the completed product.
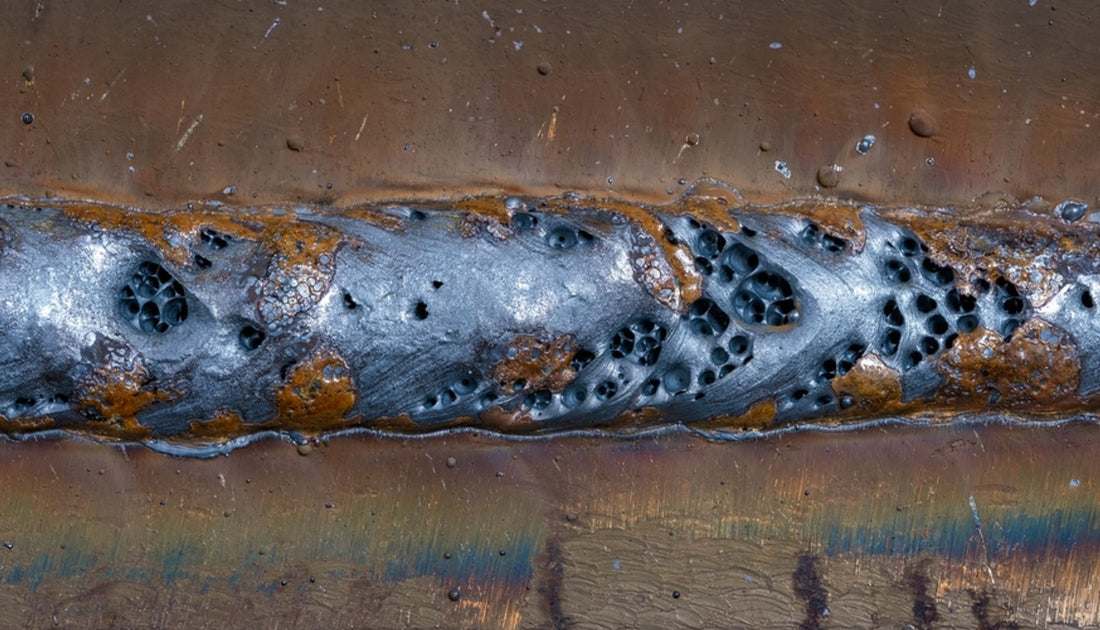
To find and measure porosity, non-destructive testing techniques such as ultrasonic testing or X-ray inspection are frequently employed. These strategies permit for the recognition of interior problems without compromising the honesty of the weld. By assessing the dimension, shape, and distribution of porosity within a weld, welders can make enlightened choices to enhance their welding processes and achieve sounder weld joints.
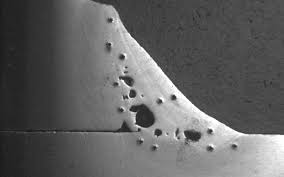
Elements Influencing Porosity Formation
The occurrence of porosity in welding is affected by a myriad of factors, ranging from gas shielding efficiency to the complexities of welding parameter setups. One critical variable adding to porosity formation is inadequate gas shielding. When the shielding gas, typically argon or CO2, is not effectively covering the weld pool, climatic gases like oxygen and nitrogen can infect the liquified steel, resulting in porosity. Furthermore, the cleanliness of the base materials plays a substantial role. Contaminants such as rust, oil, or wetness can vaporize during welding, creating gas pockets within the weld. Welding parameters, including voltage, current, take a trip rate, and electrode type, also influence porosity development. Utilizing improper setups can create extreme spatter or heat input, which subsequently can cause porosity. Moreover, the welding technique employed, such as gas steel arc welding (GMAW) or shielded steel arc welding (SMAW), can affect porosity formation as a result of variations in heat circulation and gas protection. Comprehending and controlling these variables are vital for reducing porosity in welding procedures.
Impacts of Porosity on Weld Top Quality
The visibility of porosity likewise deteriorates the weld's resistance to corrosion, as the caught air or gases within the gaps can react with the surrounding atmosphere, leading to destruction over time. Additionally, porosity can hinder the weld's capacity to hold up against pressure or influence, additional endangering the overall quality and integrity of the bonded structure. In crucial applications such as aerospace, auto, or structural buildings, where safety and durability are paramount, the harmful results of article porosity on weld top quality can have severe effects, highlighting the value of minimizing porosity with appropriate welding strategies and treatments.
Strategies to Reduce Porosity
Additionally, using the ideal welding specifications, such as the correct voltage, present, and travel speed, is critical in stopping porosity. Maintaining a consistent arc length and angle throughout welding additionally aids lower the likelihood of porosity.

Furthermore, selecting the appropriate shielding gas and keeping correct gas flow prices are necessary in minimizing porosity. Making use of the proper welding method, such as back-stepping or using a weaving movement, can additionally assist distribute warmth evenly and decrease the chances of porosity development. Making sure appropriate ventilation in the welding environment to eliminate any potential sources of contamination is vital for achieving porosity-free welds. By executing these Find Out More strategies, welders can effectively decrease porosity and generate high-grade bonded joints.
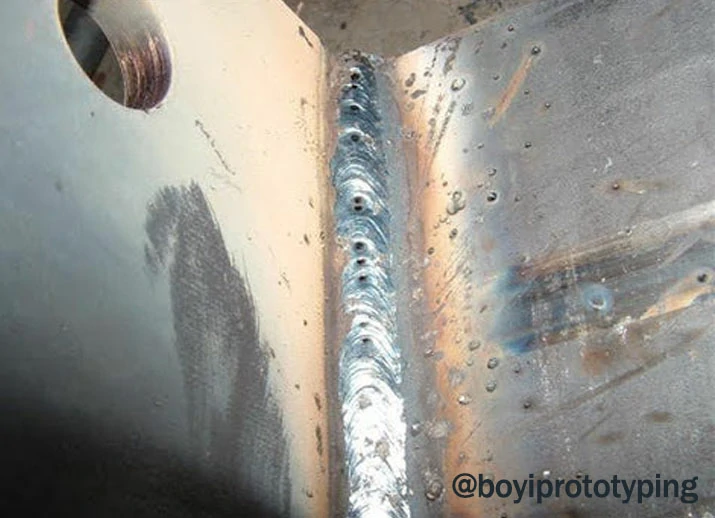
Advanced Solutions for Porosity Control
Applying advanced modern technologies and innovative approaches plays a crucial function in accomplishing premium control over porosity in welding procedures. Additionally, utilizing innovative welding techniques such as pulsed MIG welding or customized atmosphere welding can additionally help mitigate porosity problems.
An additional sophisticated solution includes making use of sophisticated welding tools. As an example, utilizing tools with integrated functions like waveform control and sophisticated power sources can improve weld high quality and minimize my explanation porosity dangers. The implementation of automated welding systems with exact control over specifications can significantly reduce porosity issues.
Moreover, including innovative tracking and evaluation technologies such as real-time X-ray imaging or automated ultrasonic testing can help in spotting porosity early in the welding procedure, enabling instant rehabilitative activities. Generally, incorporating these sophisticated services can substantially enhance porosity control and boost the general quality of bonded components.
Conclusion
In conclusion, understanding the scientific research behind porosity in welding is essential for welders and producers to produce premium welds - What is Porosity. Advanced remedies for porosity control can better enhance the welding process and make sure a solid and dependable weld.
Comments on “Exactly how to Recognize What is Porosity in Welding and Improve Your Strategy”